Panoval Label S.A. a été créée en 1991, en Suisse. S’appuyant sur les atouts de l’entreprise en Extrême-Orient, Panoval (Asie) a été créée à Hô Chi Minh-Ville, au Vietnam, en 2017. Cette installation de pointe spécialement conçue comprend plusieurs lignes de revêtement et une installation certifiée ISO Classe 6. salle blanche pour produits haut de gamme nécessitant les dernières technologies de revêtement. L’entreprise est également certifiée ISO 14644-2.

Plus de 60 % du volume mondial d’étiquettes adhésives sensibles à la pression est produit en Extrême-Orient, notamment celles destinées aux applications électroniques, médicales et pharmaceutiques. C’est la principale raison pour laquelle l’entreprise a été fondée au Vietnam, même si la propriété globale reste européenne. Bien qu’elle ne dispose que d’un seul site de production, Panoval travaille à l’international avec des revendeurs et des clients directs et a bâti une entreprise avec une présence mondiale. Leur agilité de production et leur réputation de flexibilité leur ont permis de devenir l’un des principaux fournisseurs d’étiquettes spécialisées non standard. Les clients typiques sont des revendeurs d’emballages flexibles, des transformateurs d’étiquettes et des imprimeurs conventionnels.
Panoval emploie actuellement 25 personnes et est en constante expansion. L’équipe de direction est composée de professionnels chevronnés et opérationnels à l’échelle internationale possédant une vaste expérience dans le développement et la production de stratifiés d’étiquettes pour les applications les plus exigeantes. Le directeur Wilco van Zwieten a rejoint Panoval en tant que directeur des ventes en 1993 et constitue désormais un élément clé de cette équipe. Sa mission est de stimuler de nouvelles activités et il considère le progrès technologique et l’innovation comme étant essentiels à leur succès. Comme il l’explique : « Sur un marché aussi concurrentiel, c’est la taille relativement petite de l’entreprise et l’exploitation de deux lignes de revêtement très différentes qui nous permettent de connaître autant de succès. En plus du travail courant à volume plus élevé que nous effectuons, notre équipe de production est en mesure d’exécuter une multitude de petits travaux spécialisés, changeant parfois de produit trois ou quatre fois par équipe. Nous utilisons la toute dernière technologie thermofusible UV pour sauvegarder nos systèmes à base de caoutchouc. Cette technologie UV est la seule qui puisse potentiellement remplacer les revêtements à base de solvants… pas tout de suite, mais d’ici dix à quinze ans. Pour ce faire, vous devez disposer d’une solution de durcissement UV haut de gamme, dotée de toutes les fonctionnalités nécessaires, qui soutiennent cette technologie. Et c’est ce que nous avons conçu, en collaboration avec les fabricants de machines et GEW, afin de pouvoir répondre à tous nos besoins dans les cinq à dix prochaines années. Nous sommes à l’épreuve du temps.»
Conçu et fabriqué au Royaume-Uni par GEW, le système de durcissement UV sur mesure de Panoval comprend cinq têtes de lampe NUVA2, pouvant accueillir jusqu’à sept têtes de lampe au total, montées contre un rouleau refroidi de Ø 1 000 mm sur une ligne de revêtement Sung An Machinery (SAM). Les lampes sont montées autour du tambour sur un cadre solide, séparé du rouleau et coulissant depuis sa position engagée sur des rails. Cela permet d’accéder à la surface du rouleau et au dessous de l’ensemble tête de lampe.

Lors de sa recherche initiale d’une solution de durcissement UV, van Zwieten a été orienté vers GEW par un associé malaisien qui avait récemment travaillé avec GEW pour la conception et l’installation d’un système de durcissement UV pour les applications de revêtement antiadhésif. Van Zwieten se souvient : « J’ai visité l’usine malaisienne pour voir l’installation sur place, puis j’ai commencé à parler à GEW. Au début, lentement, car nous savions que nous avions besoin d’une solution complexe et technique avec un haut niveau de personnalisation. Peu à peu, l’élan s’est construit au fur et à mesure qu’il répondait aux exigences de Panoval avec la division « Spécialiste UV » de GEW. Il commente : « Nous avons été impressionnés par les gens de GEW… leur réactivité et leur capacité à répondre à toutes nos questions, aussi techniques soient-elles. Il s’agit de travailler avec les bonnes personnes. »
Van Zwieten a ensuite visité les installations de production de GEW au Royaume-Uni pendant la construction du système, ce qui a donné aux deux parties l’occasion de discuter du système plus en détail et de s’assurer qu’il était sur la bonne voie pour répondre à toutes les exigences et attentes. Concernant la conception, l’installation et l’assistance technique continue du système, van Zwieten est sans réserve : « L’ensemble du processus s’est déroulé sans problème, nous n’avons rencontré aucun problème. Si un problème technique survient, nous disposons du système de surveillance à distance de GEW pour nous aider – mais nous avons vraiment eu une bonne expérience avec ce système. Il poursuit : « À ce jour, la seule demande que nous avons eue pour le service de surveillance à distance concerne les rapports hebdomadaires que nous recevons automatiquement, qui nous montrent des informations de gestion utiles telles que la durée de fonctionnement, les heures d’utilisation des lampes, la consommation d’énergie et l’efficacité. Cela nous apporte également une certaine tranquillité d’esprit car nous savons que si un problème survenait, il serait immédiatement signalé par la plateforme de surveillance. »
Comme le souligne van Zwieten, aucune dépense n’a été épargnée dans la spécification du nouveau système de durcissement UV, afin de garantir qu’il répondra à toutes les demandes pour les années à venir. Il commente : « Un lamineur typique installera une ou deux stations de lampes et sera ensuite satisfait. Nous nous sommes différenciés ici et avons installé une série de cinq lampes en tandem, ce qui signifie que nous pouvons modifier la distance entre l’application chimique et le durcissement d’une tâche à l’autre, ce qui nous permet de répondre à de nombreux marchés différents qui ne peuvent actuellement pas être satisfaits avec cette technologie. . C’est pourquoi nous avons choisi de travailler avec les gens de GEW, ils possèdent l’expertise technique et l’expérience nécessaire pour un système aussi complexe. Nous espérons désormais un retour sur investissement rapide, grâce aux économies d’énergie et aux nouveaux travaux que le système UV nous apporte. »
Les marchés cibles de Panoval sont les industries pharmaceutique et électronique, qui exigent une étiquette plus propre avec de faibles propriétés de dégazage résiduel. Van Zwieten explique : « Le dégazage résiduel est le cas où un produit continue d’émettre des gaz après sa production, ce qui peut constituer un problème sérieux pour les fabricants. Dans le monde de l’électronique, par exemple, les dégazages peuvent provoquer des pannes électroniques et si vous fabriquez des articles coûteux tels que des lecteurs optiques, tout facteur de panne doit être réduit au minimum absolu, s’il ne peut pas être complètement éradiqué. Il poursuit : « C’est là que le système de séchage UV nous distingue vraiment. Nous avons essayé et testé notre processus de durcissement dans notre environnement de production en salle blanche ISO 6, et nous pouvons produire des stratifiés avec des propriétés de dégazage bien inférieures. Cela nous permet d’offrir un produit plus propre et bien supérieur à ces fabricants spécialisés et à leurs transformateurs. »
Grâce au système UV sur mesure conçu spécifiquement pour Panoval, la distance entre les têtes de revêtement et les lampes de polymérisation peut être contrôlée avec précision. Cela signifie que l’exposition optimale peut être obtenue pour une multitude d’applications différentes. De plus, le système UV a été conçu avec sept boîtiers de têtes de lampe et cinq cassettes de lampes repositionnables, ce qui signifie que les têtes de lampe peuvent être placées dans un certain nombre de positions différentes, pour contrôler efficacement le temps de séjour. En augmentant le temps entre l’application des produits chimiques sur le substrat et le moment où ces produits chimiques sont durcis, cela laisse plus de temps aux gaz indésirables pour s’échapper avant le laminage. Cela affecte également la vitesse à laquelle la machine peut fonctionner ; la période de dégazage plus longue permet d’obtenir un durcissement efficace et sûr à des vitesses de fonctionnement jusqu’à 50 % plus rapides. Comme le dit van Zwieten : « Cela nous donne un énorme avantage concurrentiel sur de nombreuses entreprises américaines et européennes, qui sont limitées à fonctionner à des vitesses plus lentes. »
Démontrant la recherche de la solution parfaite par l’entreprise, Panoval a également investi dans l’installation de cinq capteurs de surveillance UV multipoints (mUVm) GEW installés sur chacune des têtes de lampe UV et reliés à leur système ERP. Ceux-ci peuvent mesurer à la position centrale de la lampe et aux bords extrêmes d’une bande de 500 mm et d’une bande de 1 050 mm. En plus des lectures du compteur de particules qui mesurent avec précision les niveaux de dégazage immédiatement après le durcissement, mUVm permet à l’équipe de production de mesurer et de vérifier que le niveau correct de dose et d’intensité UV a été administré tout au long du cycle de production. Avec mUVm, il est possible de générer un certificat de durcissement UV pour chaque lot en enregistrant les sorties UV en direct pour chaque lampe. Les données de sortie UV en temps réel sont exportées via une interface API RESTful.
Cependant, l’objectif de van Zwieten est de développer davantage les avantages du système de surveillance UV en utilisant sa capacité de reporting pour rechercher et établir des niveaux d’énergie optimaux pour l’adhérence initiale, l’adhésion et la libération de la gamme principale de produits de l’entreprise. Ces informations du capteur UV seront ensuite utilisées pour créer une carte de durcissement 3D de chaque rouleau géant de produit, offrant ainsi un haut niveau de traçabilité aux fabricants utilisateurs finaux. Si ces données sont particulièrement cruciales pour les clients des secteurs pharmaceutique, électronique et aérospatial, elles peuvent également être utilisées pour mettre en place des cycles de production répétés, rapidement et efficacement.
L’équipe de Wilco van Zwieten a également dû surmonter des difficultés techniques créées par les conditions locales à Ho Chi Minh Ville. Les 18 000 m3/h d’air utilisés pour le refroidissement sont aspirés dans la salle blanche depuis l’extérieur du bâtiment à une température ambiante d’environ 35°C. Ils ont installé une filtration en deux étapes et environ 25 mètres de conduits d’entrée supplémentaires pour réduire la température de l’air, l’humidité et les particules contaminantes à l’intérieur, avant qu’elles n’atteignent les têtes de lampe.
L’équipe de production est collectivement animée par un état d’esprit pionnier ; leur objectif est d’utiliser la recherche et le développement pour créer des produits offrant à l’utilisateur final un avantage commercial. Un exemple en est leur production de substrat pour les étiquettes de pneus, en utilisant un procédé thermofusible UV raffiné. Comme l’explique van Zwieten : « Nous n’utiliserions pas de thermofusible conventionnel pour les étiquettes de pneus car il est assez instable, en particulier avec un grammage plus élevé. Cela oblige le convertisseur à réduire la vitesse de conversion car les lames de découpe sont rapidement contaminées par l’adhésif. Au lieu de cela, nous avons perfectionné le processus de thermofusible UV grâce auquel nous pouvons légèrement surpolymériser, pour créer un adhésif à faible adhérence qui a une adhérence finale très élevée. Cela signifie que le transformateur peut produire ses étiquettes beaucoup plus rapidement et plus proprement. C’est une situation gagnant-gagnant pour nous deux. »

Ce sont les avantages commerciaux en aval qui différencient leurs produits UV des produits conventionnels et qui compensent largement le coût légèrement plus élevé des matières premières à base d’UV. En outre, van Zwieten souligne une tendance du marché qui joue également en leur faveur : « De plus en plus de fabricants de revêtements produisent des polymères à base d’UV et nous constatons que les prix chutent rapidement… ils ont déjà baissé de plus de 40 % au cours de l’année. trois dernières années. Ce n’est qu’une question de temps avant que les UV prennent le dessus. »
Le système à cinq lampes de Panoval permet à l’équipe d’adapter le processus de durcissement à chaque tâche, afin d’obtenir une sous-durcissement et une sur-durcissement à volonté. Comme l’explique van Zwieten : « Pour certains travaux, nous devons procéder à une sous-curation et nous pouvons le faire en utilisant simplement une lampe au bout du chemin. L’avantage est que cela prolonge le trajet jusqu’à 130 cm, ce qui laisse le temps au dégazage de se produire avant que le revêtement n’atteigne la station UV. Nous pouvons ainsi produire des étiquettes pour des applications médicales très exigeantes, par exemple, sans ralentir notre ligne de vernissage. »
Pour quantifier cette augmentation de vitesse en termes d’avantage concurrentiel, van Zwieten poursuit : « Nous pouvons exécuter ces travaux particuliers jusqu’à 40 mètres par minute, ce qui est bien au-dessus de la norme pour ce type de produit spécialisé. Ils fonctionnent couramment en Europe et aux États-Unis à une vitesse de 25 mètres par minute et sont par conséquent nettement plus chers sur des produits comparables. »
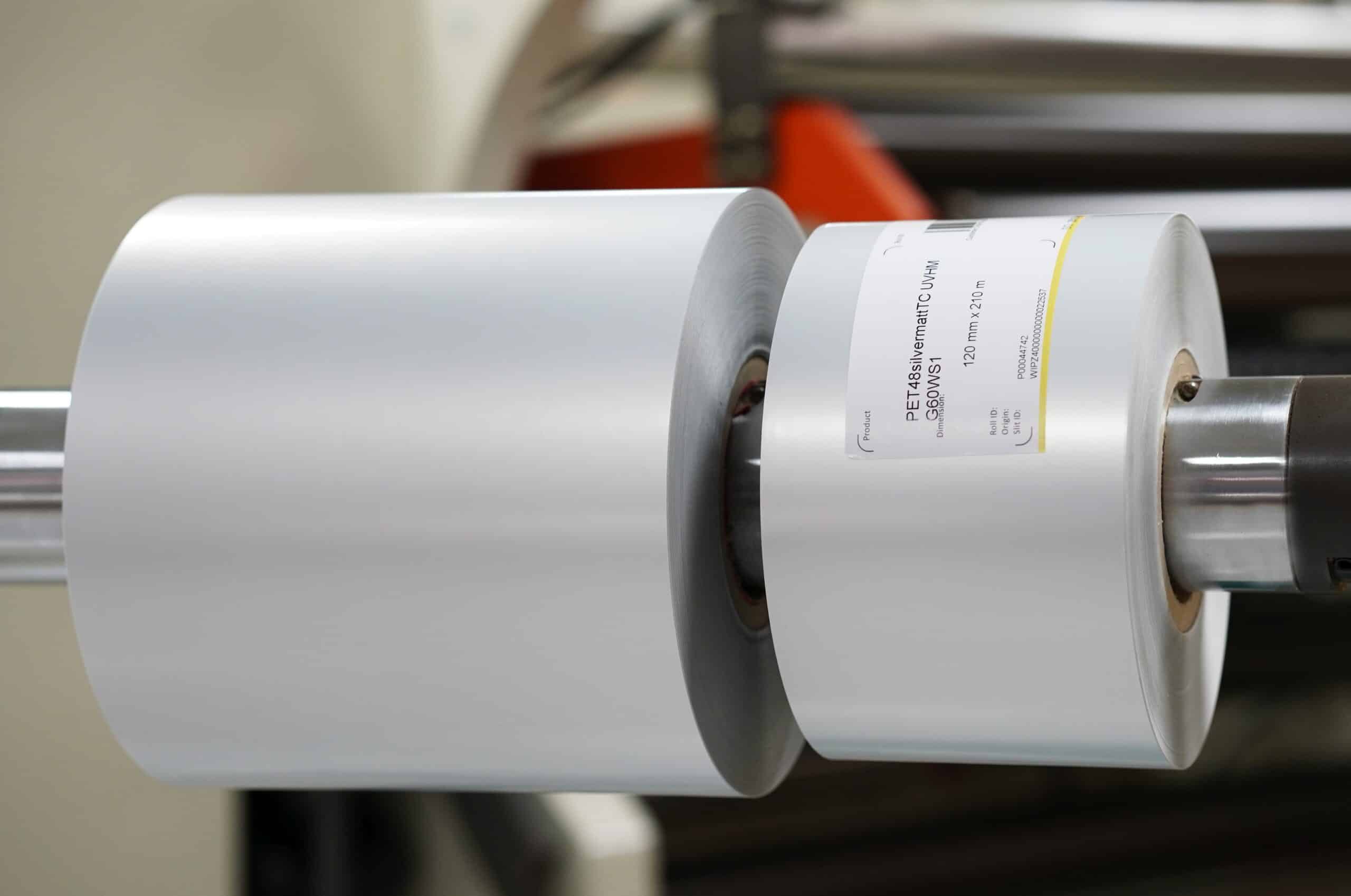
L’étiquetage pour les applications médicales est souvent requis sur des substrats non tissés, qui absorbent bien plus de rayonnements que les polyesters et les polypropylènes. Cela signifie qu’une puissance de durcissement UV élevée est également une exigence régulière, et le surdurcissement est facilement obtenu avec jusqu’à 108 kW de puissance UV disponible. Le surdurcissement UV est utilisé pour imiter les propriétés les plus souhaitables des adhésifs à base de solvants, grâce auxquels le revêtement est durci pour devenir peu collant et sec au toucher, tout en restant un adhésif hautement cohésif qui vieillit extrêmement bien. Ce procédé présente d’autres avantages, comme l’explique van Zwieten : « Le collant initial est faible et permet même un repositionnement, mais l’adhésion finale est très forte – dépassant facilement 50 newtons – comme l’exige un étiquetage haute performance. Et puis nous revenons aux avantages de la conversion, qui devient un processus beaucoup plus rapide avec les revêtements durcis aux UV. Il conclut : « Nous pouvons obtenir tous les avantages des revêtements à base de solvants, mais sans les dégazages et les extractibles, qui préoccupent tant les industries médicale, aérospatiale et électronique. »
Panoval dispose également de fenêtres en quartz GEW « HiC » installées sur les têtes de lampe UV, qui sont particulièrement adaptées aux applications thermofusibles. Cette qualité spéciale de quartz permet à beaucoup plus d’énergie UVC de passer au revêtement, par rapport au quartz conventionnel. Comme le commente van Zwieten : « Nous n’avons pas lésiné sur les spécifications de notre système UV et nous n’avons pas encore trouvé de travail qu’il ne peut pas faire. Parce que nous gérons un éventail large et diversifié de travaux exigeants et de courte durée, nous devions être sûrs que nous serons toujours en mesure de réaliser ce que nous voulons faire. Et si jamais nous constatons que nous avons besoin de plus de puissance, nous pouvons facilement ajouter deux cassettes de têtes de lampe supplémentaires dans les boîtiers vacants. Il ajoute : « Or, en l’état, nous pouvons courir à 220 mètres par minute sur cette ligne. Nous atteignons le double de la vitesse de production d’une application équivalente à base de solvant. À titre d’exemple, nous avons récemment produit une étiquette en polyester amovible avec un revêtement à faible libération de silicone à 100 mètres par minute avec une faible couverture de poids de couche et aucun dégazage… et cela, à ma connaissance, est un nouveau record du monde. »
« Le système GEW a atteint précisément ce que nous souhaitions. Il durcit parfaitement, il durcit parfaitement. Nous économisons d’énormes quantités d’électricité et réduisons notre empreinte carbone. Si vous imaginez que notre ancien système à base d’eau nécessitait près de 40 mètres de fours chauffés à 200 degrés pour évacuer l’eau… nous consommons environ 1 800 kW par heure. Avec les revêtements à base d’eau, environ 40 % de chaque kilo est constitué d’eau qui doit être extraite. Désormais, avec les UV, nous pouvons fonctionner à 220 mètres par minute et le maximum que nous consommons est d’environ 600 kW par heure. C’est donc un troisième. »
Cependant, il y a d’autres considérations à prendre en compte lors de l’adoption de processus de durcissement par UV, comme le souligne van Zwieten : « Vous avez besoin d’un personnel mieux formé et dédié pour travailler avec et comprendre les UV, et vous avez besoin d’un meilleur équipement pour commencer. À titre de comparaison, il existe plus de 1 100 plastifieuses à base de solvant rien qu’en Chine, et ce sont des machines basiques, peu coûteuses et simples à utiliser. Vous n’avez pas besoin d’un laboratoire. Mais c’est un jeu dangereux : il est toxique, polluant et coûte beaucoup d’énergie. » En comparant cela avec les avantages des UV, il conclut : « Avec les UV, vous n’avez pas besoin d’un incinérateur, ce n’est pas toxique, vous n’avez pas de risque d’incendie, et les économies d’énergie et les avantages environnementaux sont très impressionnants. » Il conclut : « Nous avons trouvé en GEW un partenaire très compétent et réactif. À tous ceux qui recherchent une solution UV pour les adhésifs thermofusibles, je suggère de les appeler. »
Cliquez ici pour plus d’informations sur notre procédé UV spécialisé.