Avec cinq sites aux États-Unis et un effectif d’environ 650 personnes, Nosco est un géant dans le monde du packaging pharmaceutique. Ils travaillent avec plus de 450 sociétés pharmaceutiques, dont 9 des 10 plus grandes aux États-Unis, et plus de 160 sociétés de santé naturelle.
Regardez la vidéo de l’étude de cas ci-dessous ou poursuivez votre lecture…
Craig Curran est président de l’entreprise appartenant aux employés et est basé au siège social de Nosco et au centre d’innovation de l’emballage de 270 000 pieds carrés à Pleasant Prairie, dans le Wisconsin. Il donne un bref historique du développement de Nosco jusqu’à ce qu’elle en soit aujourd’hui : « Eh bien, Nosco est en fait une entreprise vieille de 120 ans. Nous avons été fondés en 1906 par une famille locale. Ils travaillèrent dans le secteur des fournitures de bureau jusqu’en 1932, lorsque [le docteur] M. Abbott leur demanda de reprendre son emballage de médicaments pharmaceutiques. Cela a lancé l’entreprise sur une toute nouvelle trajectoire. C’est ainsi que l’entreprise s’est développée et nous sommes passés des étiquettes aux cartons, puis aux emballages flexibles… nous fabriquons en fait des milliards d’étiquettes, de cartons et d’encarts chaque année. »

La liste de clients enviables de Nosco s’est constituée régulièrement au fil de nombreuses années. L’entreprise est fière d’offrir des services innovants et complets qui aident à fidéliser les clients existants et à en attirer de nouveaux, comme l’explique Curran : « Nous faisons affaire avec les principaux clients pharmaceutiques depuis des décennies. Nous servons également des produits de santé naturels et certains produits de consommation. Ils viennent chez Nosco, en réalité, grâce à notre groupe d’ingénierie de solutions, un groupe d’ingénieurs en emballage qui aident nos clients à concevoir l’emballage dès le début. Ainsi, si un nouveau médicament ou un nouveau produit doit arriver sur le marché, nous travaillons en partenariat avec le client afin de devenir réellement un guichet unique. »
Il conclut : « Le résultat final est que les grands clients pharmaceutiques comme Abbott ou AbbVie, Takeda, Otsuka, Astellas, restent et font des affaires ici parce que nous sommes en mesure de les soutenir avec ce type de service. »
Le passage au séchage LED à Pleasant Prairie
Nosco dispose actuellement de deux presses Komori installées avec des systèmes de durcissement UV GEW. L’un se trouve dans les installations de Pleasant Prairie, tandis que le second est situé dans l’usine de production de Nosco à Bridgeview, dans l’Illinois. Les deux systèmes sont assez différents dans leurs spécifications car chacun a été conçu précisément pour le travail à effectuer, tout en incluant en même temps l’infrastructure nécessaire pour leur permettre d’être facilement adaptés ou étendus à l’avenir, si nécessaire.
Lee Marcoe, responsable des opérations stratégiques chez Pleasant Prairie, explique la réflexion détaillée qui a été menée pour équiper leur presse avancée Komori, une GLX940RP-A : « Avec l’ajout de notre nouvelle Komori, nous avons opté pour une RP 9 couleurs configurée en 8 sur 1 avec une coucheuse sur le dessus. L’inconvénient d’une seule couleur est déjà équipé de notre lampe UV GEW LED, mais nous avons jeté un petit coup d’œil à ce que nous pourrions vouloir être demain. Il s’agissait d’un investissement important pour l’entreprise. Certains de nos clients sont avec nous depuis 40 ans et plus. Tous n’étaient pas prêts à opérer un changement complet vers le LED/UV. Beaucoup de leurs produits datent de plusieurs années et ils fonctionnent avec les œuvres d’art dont ils disposent, et il faut beaucoup de temps, très honnêtement, pour apporter certains de ces changements. Nous voulions nous assurer qu’au cours des 10 années où nous aurons cette machine, nous aurons la capacité de nous adapter et d’être en mesure de fournir les services dont nos clients auraient besoin à l’avenir, s’ils devaient changer. »
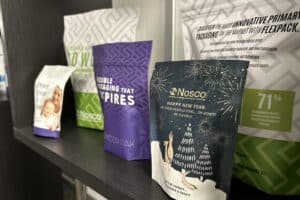
« À l’origine, GEW ne devait pas faire partie de l’installation de la machine, mais nous avons en fait passé pas mal de temps avec notre partenaire Komori pour décider quelles étaient les meilleures options. Ce que nous avons vraiment trouvé intéressant, c’est que GEW a fait beaucoup d’innovations intéressantes. »
« Nous avons rencontré les ingénieurs de GEW pour déterminer quelle était la meilleure façon de construire cette presse. Et il possède en fait toute l’infrastructure nécessaire pour l’équiper entièrement en LED/UV. Nous pouvons le faire au niveau de la livraison et de toutes les unités d’impression en haut, en plus de ce qui est déjà en bas. »
« Mais nous voulions nous assurer que si les choses commençaient à changer, nous avions la flexibilité de placer nos réseaux de LED dans toutes les unités d’impression avec les UV ordinaires, car parfois certaines encres, certains vernis pourraient mieux réagir aux UV. Mais avoir la possibilité d’aller et venir nous permet beaucoup plus de flexibilité car, encore une fois, nous sommes parfois à la merci de nos consommables. Nous apprécions donc vraiment l’adaptabilité et la polyvalence dont dispose GEW pour pouvoir fonctionner soit ou. »
Le passage au séchage UV et LED à Bridgeview
Dans l’usine Nosco de Bridgeview dans l’Illinois, la presse Komori advance GLX-840A est configurée avec une combinaison de têtes de lampe GEW Arc et LED, pour une productivité et une polyvalence optimales.
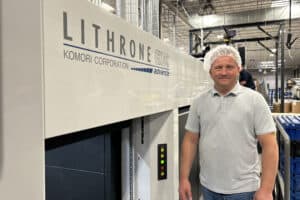
Peter Janik, directeur d’usine chez Bridgeview, commence par expliquer les raisons pour lesquelles ils ont choisi GEW et leur besoin de changement : « GEW a été l’un de nos fournisseurs pendant de nombreuses années parce que nous utilisions les systèmes GEW sur les presses à laize étroite. GEW a développé et construit des systèmes pour presses d’impression lithographique de 40 pouces, ce qui a donc été un facteur important lors de notre choix. Le système précédent qui équipait cette presse avait déjà 10 ans et était entièrement UV, consommant beaucoup d’énergie. Nous recherchions donc de meilleures solutions en termes d’économies d’encre et également d’énergie. Nous recherchions des moyens modernes et innovants pour soigner notre produit. »
« Avant, nous imprimions de manière conventionnelle, puis prenions ces feuilles et appliquions la finition UV sur la machine hors ligne. Nous avons éliminé cela en plaçant le GEW sur notre presse à imprimer et en faisant tout cela en un seul passage. Cela signifie donc que nous avons éliminé beaucoup de gaspillage… perte de temps, gaspillage de produit. Les économies de coûts sont donc assez substantielles. »
« Le système que nous avons actuellement sous presse est un combo. L’encre est durcie par des lampes LED et les revêtements sont durcis par des [lampes} au mercure. Cette presse dispose de huit groupes d’impression. Nous n’avons que deux lampes LED pour ces huit unités, mais chacune a son propre portail où nous pouvons brancher la lampe, afin que l’opérateur puisse déplacer cette lampe où il le souhaite. »
« Le système GEW est un système auxiliaire qui n’interfère pas avec l’impression conventionnelle. Ainsi, vous pourriez avoir les deux systèmes sur la presse à imprimer, tout comme nous l’avons actuellement sur notre 840, nous avons des lampes IR conventionnelles et nous avons également GEW. »
Changement pour le mieux
Chez Pleasant Prairie, Lee Marcoe décrit les avantages qu’il a constatés avec l’introduction du polymérisation par LED : « Eh bien, ici, tout fonctionnait de manière conventionnelle, tout ce que nous avions. Nos deux presses Heidelberg étaient donc des machines tout à fait conventionnelles. »
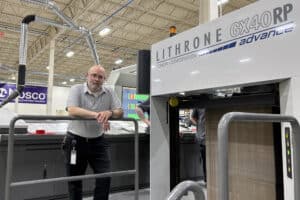
« Si nous devions imprimer une seule couleur ou une couleur au verso, nous devrions la faire passer en deux passages sur nos presses conventionnelles. Parfois, il faudrait faire un peu attention à ne pas trop encrer parce que cela donnerait lieu à des maculages, des marquages, des éraflures, des choses en aval, ce ne serait pas préférable. Mais maintenant, avec nos LED, nous n’avons plus besoin d’être aussi conscients de nos densités et nous pouvons réellement pousser la couleur pour lui donner un effet un peu plus vibrant. »
« Et comme le durcissement est instantané du côté négatif, nous obtenons une très bonne pose sur le côté denté non couché de la feuille. Ainsi, non seulement la qualité s’est améliorée, et c’est une amélioration significative, mais l’efficacité s’améliore en aval. La réponse la plus courte est donc qu’avant, nous prenions deux fois plus de temps pour faire quelque chose et que cela n’avait pas l’air aussi bien. Maintenant, les choses semblent bien meilleures et nous y parvenons en presque deux fois moins de temps. »
Marcoe souligne les avantages contrastés des deux sites : « Dans notre environnement de Bridgeview, nous ciblons certainement les entreprises ayant plus d’embellissements et des besoins d’impression plus complexes parce que nous disposons là-bas de la machine avec toutes les capacités. Dans notre environnement, ce que nous avons vraiment visé avec cette machine, c’est d’être plus efficace et d’être capable d’exécuter une productivité en un seul passage et d’obtenir ces avantages en matière de débit sans sacrifier du tout la qualité. »
“Cela nous permet donc de cibler de nouvelles affaires, et cela nous permet également de reprendre nos activités existantes et de devenir plus rentables avec elles. »
Retour sur investissement et installation
Avec trois têtes de lampe GEW E4C Arc livrées avec la presse et deux têtes de lampe LeoLED qui peuvent être déplacées vers l’une des huit stations inter-ponts, le système UV de Bridgeview est une pièce d’ingénierie sophistiquée qui a nécessité un investissement important. Concernant le retour attendu sur cet investissement, Peter Janik commente : « Nous avons fait notre propre retour sur investissement, je n’ai pas de chiffres exacts, c’est dans la comptabilité, mais le retour sur investissement est en fait très bon et je pense que le système a été déjà payé, après un an. »
Malgré la complexité de l’installation du système UV à Bridgeview, elle a été soigneusement planifiée par GEW et Nosco pour minimiser les interruptions et les temps d’arrêt de la production, comme l’explique Janik : « L’ensemble du processus a été très simple car GEW avait une approche très professionnelle du point de vue commercial. , point de vue technique. L’installation a été rapide. Au bout d’une semaine, seuls les techniciens américains étaient sur place et sont restés avec nous quelques jours, juste pour s’assurer que tout se passait bien. »
En résumé
Lee Marcoe est philosophique quant à la transition vers le polymérisation par LED et donne des conseils judicieux à tous ceux qui envisagent une démarche similaire : « Où voulez-vous être dans cinq ans ? Où veux-tu être dans 10 ans ? Parce que ces types d’investissements peuvent être importants et que vous ne voulez pas vous mettre dans une position où vous ne pouvez pas être polyvalent et vous adapter. Si je parlais à quelqu’un qui s’y lance pour la première fois, je l’exhorterais à vraiment réfléchir à ce qu’il pense être, car il devient alors plus facile de choisir avec qui vous souhaitez vous associer pour cela. »
« Et je sais que c’était un choix assez facile pour nous. Nous avons regardé assez loin dans le terrier du lapin pour voir… où pensons-nous que nous serons dans cinq ou dix ans ? Et nous voulions nous associer à une entreprise comme GEW pour nous assurer que nous avions l’adaptabilité et la polyvalence nécessaires pour faire tout ce que nous devions faire. »
À Bridgeview, Peter Janik revient sur la décision d’installer un système de polymérisation hybride UV et LED : « Je suis très heureux de l’avoir fait. Oui. C’est un de ces moments où lorsque vous avez un problème avec une voiture et que vous en achetez une nouvelle, les problèmes disparaissent et personne n’en parle. Même chose ici. Lorsque nous avons installé ce nouveau système, personne n’a eu de problème. »
« Il n’y a donc aucun problème, vous savez, l’opérateur arrive, aucun problème avec le système. Le produit a l’air bien. Vous savez, nous avons pu obtenir plus de produits grâce à ce système. »
« C’est donc une expérience formidable. »
Pour en savoir plus sur les systèmes de durcissement LeoLED2 de GEW pour presses à feuilles, cliquez ici.
Avec nos remerciements à Nosco : https://www.nosco.com/