Science du durcissement par UV
Le durcissement fait référence aux réactions chimiques qui se produisent pendant les processus de polymérisation. Les processus de polymérisation impliquent la liaison ou la réticulation de molécules déconnectées et de chaînes polymères plus courtes afin qu’elles forment des chaînes polymères beaucoup plus longues, plus dures et plus rigides. Bien que de nombreuses substances aient des structures polymères, la chimie et l’ingénierie des polymères se concentrent principalement sur les matériaux et les processus impliquant les plastiques et les caoutchoucs.
Si vous avez des questions concernant la terminologie utilisée ici, vous pouvez consulter notre article sur la terminologie du durcissement UV pour en savoir plus.
Le durcissement fait référence aux réactions chimiques qui se produisent pendant les processus de polymérisation. Les processus de polymérisation impliquent la liaison ou la réticulation de molécules déconnectées et de chaînes polymères plus courtes afin qu’elles forment des chaînes polymères beaucoup plus longues, plus dures et plus rigides. Bien que de nombreuses substances aient des structures polymères, la chimie et l’ingénierie des polymères se concentrent principalement sur les matériaux et les processus impliquant les plastiques et les caoutchoucs.
La photopolymérisation UV, également connue sous le nom de durcissement par rayonnement ou simplement durcissement par UV, est une catégorie spécifique de polymérisation dans laquelle l’énergie ultraviolette entraîne la réticulation au sein de matériaux formulés aux UV tels que les encres, les revêtements, les adhésifs et les extrusions. La technologie est utilisée avec succès depuis près de trois quarts de siècle dans divers processus de fabrication couvrant de nombreuses industries différentes. En effet, le durcissement UV produit des propriétés matérielles hautement souhaitables avec des installations rapides et à faible encombrement qui transforment instantanément et efficacement les matériaux humides au toucher en structures solides sèches au toucher.
Dans de nombreuses applications, les formulations UV sont constituées de matériaux entièrement solides ou à haute teneur en solides qui ne contiennent pas de supports liquides. Les particules solides sont tout simplement suffisamment petites et nombreuses pour être appliquées sur une large gamme de surfaces comme s’il s’agissait de liquides. Alors que les utilisateurs et les fournisseurs industriels décrivent parfois le changement structurel rapide du séchage UV comme un séchage, les encres, revêtements et adhésifs formulés aux UV ne sont pas séchés. Ils sont guéris.
En revanche, les formulations conventionnelles à base d’eau et de solvant incorporent de véritables supports liquides dont le but principal est de faciliter l’application de la teneur en solides souhaitée sur les surfaces prévues par diverses méthodes d’impression, de pulvérisation, de revêtement et de distribution. Une fois appliqué, le travail du support est terminé et il doit être évaporé ou séché à l’aide d’air pulsé ou de séchoirs thermiques. Après évaporation, seules les particules solides restent à la surface de la pièce, du substrat ou de la construction. Dans le cas des supports de solvants, les réglementations exigent souvent que les vapeurs de solvants évaporés soient brûlées après les brûleurs avant d’être rejetées dans l’environnement.
Pour de nombreux processus à base d’eau et de solvants qui n’utilisent pas la lumière UV pour le durcissement, de longs tunnels de séchage et des fours énergivores doivent être intégrés aux lignes de production pour stimuler activement l’évaporation. Contrairement au durcissement par UV, les processus de séchage n’entraînent pas de modifications moléculaires au sein de la chimie. Ils laissent simplement derrière eux des solides résiduels déconnectés qui reposent directement sur la surface de matériaux non poreux tels que le plastique et le métal ou sont légèrement absorbés dans des structures poreuses telles que le bois et le papier. Les solides résiduels sont souvent sujets aux rayures, aux rayures, aux éraflures, à la destruction chimique et aux intempéries. Dans de nombreux cas, des revêtements de finition transparents ainsi que d’autres mécanismes de protection tels que le laminage de films doivent être utilisés avec des matériaux à base d’eau et de solvants.
Avec le durcissement aux UV, de longues chaînes de polymères et des structures moléculaires incroyablement solides se traduisent par des propriétés physiques, mécaniques et esthétiques hautement souhaitables qui améliorent finalement l’apparence générale, la qualité et les performances de nombreux objets du quotidien. En conséquence, le durcissement aux UV est largement utilisé par les fabricants pour produire des couleurs d’encre éclatantes ; effets spéciaux visuels, tactiles et haptiques ; des liens de destruction incroyablement forts ; résistance chimique et aux intempéries supérieures ; et des qualités de surface souhaitables telles que la dureté, le glissement et la résistance aux chocs. Le durcissement aux UV est respectueux de l’environnement dans la mesure où il élimine les fours et tunnels de séchage consommateurs d’énergie, les composés organiques volatils (COV) et les polluants atmosphériques dangereux (PAD). Étant donné que les processus de durcissement aux UV propagent la réticulation chimique en fractions de seconde et que la réaction est complète à la fin, le traitement post-durcissement, la conversion, l’emballage, l’assemblage, le remplissage et l’expédition sont tous possibles immédiatement après la station de durcissement aux UV finale.
Science de la lumière
Le spectre électromagnétique représente la gamme continue de toute la lumière dans l’univers, y compris la lumière émise par les objets sur terre ainsi que par les corps célestes. Étant donné que la lumière rayonne toujours vers l’extérieur à partir d’une source émettrice, elle est souvent appelée rayonnement électromagnétique ou simplement rayonnement. Une représentation graphique du spectre électromagnétique est présentée dans l’illustration suivante.
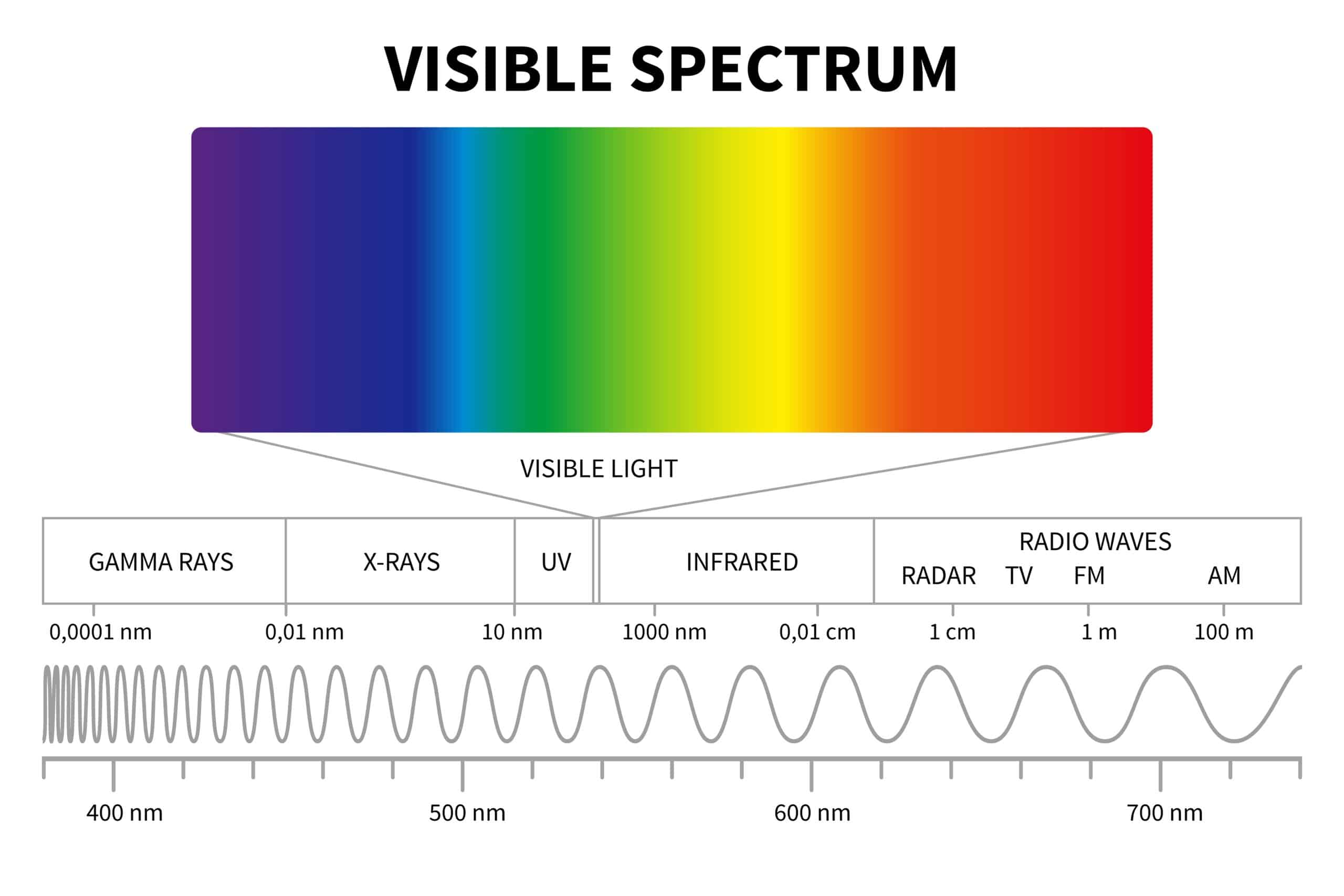
Le spectre électromagnétique est segmenté en rayons gamma, rayons X, ondes ultraviolettes, visibles, infrarouges et radio. La bande passante ultraviolette est divisée en UV sous vide, UVC, UVB, UVA et UVV. Les ondes radio sont subdivisées en radar, TV, FM et AM, les micro-ondes étant distinguées comme un sous-segment plus petit du radar et plus fréquemment comme une bande distincte entre les ondes infrarouges et radio. Chaque tranche du spectre est discrètement quantifiée par longueur d’onde, fréquence et énergie photonique. À l’exception de la lumière visible, qui produit de la couleur lors de l’interaction avec des objets, toute la lumière du spectre est invisible.
Les frontières entre les bandes de lumière ne sont pas rigides et il n’existe pas de longueurs d’onde officiellement établies auxquelles l’une se termine et l’autre commence. En conséquence, différentes industries, organisations, normes et instruments de mesure font référence à des plages légèrement différentes. Aux fins du durcissement aux UV, les plages suivantes sont généralement utilisées.
- UV sous vide (100 – 200 nm) – partie du spectre électromagnétique comprise entre 100 et 200 nm. Les longueurs d’onde UV sous vide sont ainsi nommées car elles se propagent mieux dans le vide et ne voyagent pas dans l’air. Les UV sous vide émis par les systèmes de durcissement ne sont efficaces dans les processus de photopolymérisation que lorsque les systèmes UV et les surfaces de durcissement fonctionnent dans des environnements inertés à l’azote. En fonction de la concentration en oxygène de l’environnement inerté, il est possible que les UV sous vide génèrent de l’ozone.
- UVC (200 – 280 nm) – partie du spectre électromagnétique comprise entre 200 et 280 nm. Les UVC sont communément appelés UV courts ou UV germicides et sont invisibles à l’œil humain. L’ozone est généralement produit à des longueurs d’onde UVC de 240 nm et moins. Les longueurs d’onde UVC sont absorbées à la surface de la chimie UV et entraînent le durcissement de la surface.
- UVB (280 – 315 nm) – partie du spectre électromagnétique comprise entre 280 et 315 nm. Les UVB sont invisibles à l’œil humain. Les longueurs d’onde UVB pénètrent plus profondément dans la chimie que les UVC, mais pas aussi loin que les UVA et UVV.
- UVA (315 – 400 nm) – partie du spectre électromagnétique comprise entre 315 et 400 nm. Les UVA représentent la plus grande partie de l’énergie UV et sont communément appelés UV longs. Les UVA se situent à la limite inférieure de ce que l’œil humain perçoit comme couleur. Les longueurs d’onde UVA pénètrent profondément dans la chimie UV.
- UVV (400 – 450 nm) – partie du spectre électromagnétique comprise entre 400 et 450 nm. Le V signifie visible puisque ces longueurs d’onde sont perçues comme une couleur par l’œil humain et chevauchent une petite partie du spectre visible. Les longueurs d’onde UVV pénètrent profondément dans la chimie UV.
- ultraviolet (100 – 450 nm) – partie du spectre électromagnétique comprise entre 100 et 450 nm. La frontière entre les longueurs d’onde UV et visible n’est pas définie avec précision et est généralement considérée comme se situant entre 400 et 450 nm. Les longueurs d’onde UV sont juste au-delà de ce que l’œil humain perçoit comme la couleur violette.
- visible (400 – 700 nm) – partie du spectre électromagnétique comprise entre 400 et 700 nm. La lumière visible contient toutes les nuances de couleur, et différentes couleurs sont générées par différentes longueurs d’onde ou combinaisons de longueurs d’onde réfléchies par les objets. Le spectre visible est souvent représenté par un arc-en-ciel.
- infrarouge (700 nm – 0,1 mm) – partie du spectre électromagnétique comprise entre 700 nm et 0,1 mm. Les longueurs d’onde infrarouges sont juste au-delà de ce que l’œil humain perçoit comme la couleur rouge. Certaines longueurs d’onde infrarouges émettent de la chaleur, d’autres non. Les longueurs d’onde infrarouges constituent le facteur dominant de la chaleur rayonnée par les systèmes de polymérisation UV à électrodes et par micro-ondes. Les systèmes de polymérisation par LED UV relativement monochromatiques n’émettent pas d’infrarouge.
- micro-ondes (0,1 mm – 10 cm) – une bande étroite comprise entre 0,1 mm et 10 cm située au bord du radar et dans la partie beaucoup plus large des ondes radio du spectre électromagnétique. Les micro-ondes peuvent être exploitées pour alimenter un type spécifique de lampe de polymérisation UV utilisée dans les systèmes de polymérisation sans électrode ou par micro-ondes.
Alors que les sources UV à lampes à large bande conventionnelles telles que les à micro-ondes et à arc à électrodes émettent des UVA, des UVB, des UVC et des UVV ainsi que du visible et de l’infrarouge, les sources de polymérisation à LED dans le commerce émettent des bandes relativement étroites d’UVA plus proches du visible (365, 385, 395, et 405 nm). En conséquence, la chimie UV à large spectre formulée de manière conventionnelle ne durcit généralement pas bien avec les LED UV et doit être reformulée pour durcir uniquement avec des longueurs d’onde UVA et UVV plus longues. Heureusement, les fabricants d’encres, de revêtements et d’adhésifs conçoivent de plus en plus de produits chimiques LED UV de telle sorte qu’une seule formulation puisse être polymérisée avec des lampes LED et conventionnelles. Au cours des années à venir, de plus en plus de formulations évolueront vers cette capacité de double durcissement et entraîneront la transition progressive mais inévitable de l’industrie vers le durcissement par LED UV.
Longueur d’onde, fréquence et énergie photonique
Chaque tranche du spectre électromagnétique est discrètement quantifiée par longueur d’onde, fréquence et énergie photonique. La longueur d’onde est une mesure de la distance entre les points correspondants sur une onde lumineuse périodique. Il est généralement désigné par la lettre grecque lambda (l). La fréquence est la vitesse à laquelle une longueur d’onde spécifique apparaît. Elle est mesurée en cycles par seconde ou Hertz (Hz) et est généralement représentée par les lettres (f) ou (v). La fréquence et la longueur d’onde sont liées par la vitesse de la lumière, la fréquence étant la vitesse de la lumière divisée par la longueur d’onde. À mesure que les longueurs d’onde s’allongent, la fréquence diminue. À l’inverse, plus les longueurs d’onde diminuent, plus la fréquence augmente.
La fréquence et la longueur d’onde peuvent être utilisées pour calculer l’énergie de tous les rayonnements électromagnétiques du spectre. Ceci est accompli en utilisant l’une des deux formules équivalentes suivantes connues sous le nom de relation de Planck-Einstein.
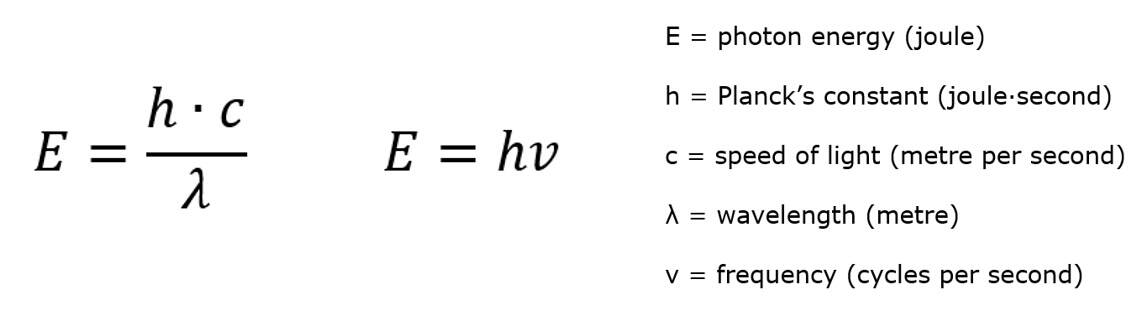
Où:
E = énergie photonique (joule)
h = constante de Planck (joule·seconde)
c = vitesse de la lumière (mètre par seconde)
λ = longueur d’onde (mètre)
v = fréquence (cycles par seconde)
Selon la relation Planck-Einstein, les longueurs d’onde plus courtes telles que les UVC ont plus d’énergie que les longueurs d’onde plus longues telles que les UVA. Par extension, toutes les longueurs d’onde de la bande ultraviolette ont considérablement plus d’énergie que les ondes visibles, infrarouges, micro-ondes et radio, tout en ayant moins d’énergie que les rayons X et les rayons gamma.
Irradiation (W/cm2)
L’irradiance est la puissance radiante arrivant sur une surface par unité de surface. Elle est exprimée en watts ou milliwatts par centimètre carré (W/cm2 ou mW/cm2). D’autres termes couramment utilisés pour désigner l’irradiance incluent la densité de puissance et la densité de watt. Bien que techniquement incorrect, l’irradiance est largement appelée intensité, et chaque fois que l’intensité est utilisée, elle est généralement comprise comme signifiant irradiance. L’irradiance est généralement mesurée et signalée comme la valeur maximale la plus élevée sur une large gamme de longueurs d’onde ultraviolettes ou comme des valeurs maximales dans chacun des segments les plus étroits des UVC, UVB, UVA et UVV. L’irradiance doit toujours être référencée au radiomètre utilisé pour la mesure ainsi qu’à l’emplacement du radiomètre par rapport à la source UV.
Pour une distance définie entre une surface de polymérisation et un système de polymérisation UV, l’irradiance est fixe pour chaque réglage de puissance de la lampe et est indépendante de la vitesse de la ligne de production ou du temps d’exposition. En d’autres termes, l’irradiance au niveau de la surface de durcissement augmente avec l’augmentation de la puissance de la lampe et diminue avec la diminution de la puissance de la lampe. La valeur de cet éclairement énergétique reste constante sur la surface de polymérisation, quelle que soit la vitesse de ligne, à condition que le réglage de la puissance de la lampe et la distance ne changent pas.
Pour les systèmes de durcissement par LED UV pour verre plat et les lampes à vapeur de mercure avec profils d’inondation, l’irradiation est affectée par la distance entre chaque point de la surface de durcissement et la tête de lampe. Dans les deux cas, des distances plus grandes entraînent des irradiations plus faibles au niveau de la surface durcie. En effet, les rayons de lumière rayonnée se propagent ou s’écartent les uns des autres à mesure qu’ils s’éloignent de la source émettrice. Cela diminue la concentration de lumière et réduit l’irradiance. Dans le cas des lampes à vapeur de mercure focalisées, l’irradiance est plus grande à la distance focale et diminue à mesure que la surface de durcissement est déplacée à l’intérieur ou à l’extérieur de la distance focale. Le but d’une lampe à vapeur de mercure focalisée est de concentrer la majeure partie de l’énergie UV rayonnée sur une bande étroite afin d’augmenter l’ampleur absolue de l’irradiance.
Dans les situations de production, la plupart des surfaces durcissantes sont exposées à un rayonnement dynamique. Un rayonnement dynamique se produit lorsqu’une tête de lampe passe sur une surface de polymérisation sans pause ou lorsqu’une surface de polymérisation passe sous une tête de lampe sans pause. À mesure que des emplacements ponctuels sur la surface de durcissement se rapprochent, s’opposent et s’éloignent d’une source UV, l’irradiation maximale correspondante à chaque emplacement et à chaque instant varie.
Un profil d’irradiation dynamique peut prendre de nombreuses formes, mais il existe généralement sous la forme d’une courbe en cloche illustrée dans l’illustration graphique suivante. Dans le graphique, chaque point du profil d’irradiance capture l’irradiance maximale à chaque instant, le haut de la courbe en cloche illustrant le moment où la surface de durcissement passe à travers la zone focale d’une lampe à vapeur de mercure ou à travers le centre d’un UV. Lampe LED. Les sources avec un éclairement énergétique maximal plus élevé ont un pic de profil plus haut. Les sources avec une irradiance maximale inférieure ont un pic de profil plus court. La largeur du profil dépend de la largeur de la tête de lampe UV ainsi que de la vitesse de la ligne de traitement ou du temps d’exposition.

Densité énergétique (J/cm2)
La densité énergétique est l’énergie radiante totale arrivant sur une surface par unité de surface et est exprimée en J/cm2 ou mJ/cm2. La densité énergétique est l’intégration de l’irradiance (W/cm2 ou mW/cm2) sur la durée d’exposition. Ceci est représenté par la zone sous le profil d’irradiance, comme indiqué dans l’image précédente. Le temps d’exposition, et par conséquent la densité d’énergie ou la surface sous la courbe, est augmenté en ralentissant la vitesse de ligne, en augmentant le temps de séjour, en ajoutant des sources de durcissement supplémentaires ou en utilisant des têtes plus larges dans le cas des LED UV. Graphiquement, ces actions répartissent la largeur de la courbe en forme de cloche sur une plus grande période de temps, aplatissent le pic ou créent plusieurs pics distincts lorsque plusieurs têtes de lampe sont utilisées en série.
Pour une application de durcissement donnée, une fois que la puissance spectrale correcte et le seuil d’irradiation minimal sont délivrés à la surface de durcissement, le facteur le plus critique affectant la vitesse et le degré de durcissement est la densité d’énergie. Alors que l’irradiance est le taux de transfert d’énergie ou de puissance, la densité énergétique est l’énergie totale délivrée. Les sources de polymérisation UV qui fournissent une plus grande densité d’énergie permettent un polymérisation à des vitesses de ligne plus rapides que les systèmes de polymérisation avec des densités d’énergie plus faibles.
Bien que techniquement incorrecte, la densité énergétique est communément appelée dose, et chaque fois que dose est utilisée, elle est généralement comprise comme signifiant densité énergétique. Pour plus de clarté, la densité énergétique est l’énergie délivrée tandis que la dose est l’énergie absorbée. L’énergie absorbée est extrêmement difficile à quantifier en pratique ; tandis que la densité énergétique peut être estimée à l’aide de radiomètres UV et de bandelettes de test de densité énergétique. Il est toujours important de noter la vitesse du compteur et de la ligne lors de la communication des valeurs de densité d’énergie obtenues grâce aux radiomètres.
Chimie du durcissement UV et photopolymérisation
Les réactions chimiques du durcissement UV reposent sur des photoinitiateurs dispersés dans des encres, des revêtements, des adhésifs et des extrusions spécialement formulés. Lorsque les photoinitiateurs sont exposés à des longueurs d’onde de lumière comprises entre 100 et 450 nm, ils absorbent l’énergie UV et produisent soit des radicaux libres, soit des espèces cationiques. Les espèces excitées conduisent des réactions par initiation, propagation et terminaison, ce qui modifie rapidement la structure moléculaire des composants de la matière première. Les applications de durcissement par UV utilisent principalement des mécanismes de durcissement par radicaux libres, les applications cationiques ne constituant que quelques pour cent de toute la chimie durcissable par UV.
Le durcissement par radicaux libres génère des radicaux libres qui entraînent des réactions de réticulation. Une exposition continue et directe aux UV en ligne de mire est nécessaire pour initier et propager la guérison des radicaux libres. Les réactions se terminent rapidement en une fraction de seconde et donnent naissance à de nouvelles formes matérielles dotées de propriétés souhaitables. La chimie des radicaux libres peut être sensible à l’oxygène, en particulier au niveau de la surface de polymérisation. Les molécules d’oxygène privent le processus de durcissement des radicaux libres et/ou diminuent la force des radicaux libres. L’augmentation de l’irradiation de la lampe, le durcissement dans un environnement azoté et la modification de la chimie sont des outils largement utilisés pour contrer l’inhibition de l’oxygène.
Un mécanisme de durcissement alternatif et moins utilisé est le durcissement cationique. Cette réaction génère des cations qui conduisent à la réticulation. Dans le durcissement cationique, une exposition aux UV est nécessaire pour initier le durcissement, mais la propagation se déroule sans exposition directe ou totale aux UV en visibilité directe. En fonction de la chimie et de l’application, les processus de durcissement cationiques se propagent sur des minutes, des heures, voire des jours avant de se terminer complètement. La chimie cationique est sensible à l’humidité et à la température, qui peuvent interférer avec la réticulation. En conséquence, les conditions environnementales ambiantes doivent être surveillées et contrôlées lors de l’utilisation de produits chimiques cationiques.
Les formulations durcissables aux UV, qu’elles soient radicalaires ou cationiques, sont formulées à partir de matériaux disponibles dans le commerce. Bien que la sélection soit plutôt diversifiée, la plupart des matières premières sont regroupées selon les types suivants.
- photoinitiateurs – molécules qui absorbent l’énergie ultraviolette sur une gamme définie de longueurs d’onde et déclenchent des réactions photopolymères par la création de radicaux libres ou de cations. Les photoinitiateurs représentent 0,5 à 15 % de la formulation UV totale en poids.
- monomères – types de molécules de résine de poids moléculaire relativement faible et de structure simple, capables de se lier à elles-mêmes ou à d’autres molécules similaires pour former des polymères réticulés aux UV. Les monomères sont des diluants réactifs utilisés pour ajuster la viscosité globale et influencer les propriétés du matériau durci. Les monomères peuvent représenter jusqu’à 50 % du poids total de la formulation et, en de rares occasions, peuvent être remplacés en partie ou entièrement par de l’eau ou un solvant.
- Oligomères – types de molécules de résine de poids moléculaire relativement faible et de structure simple, capables de se lier à elles-mêmes ou à d’autres molécules similaires pour former des polymères réticulés aux UV. Les oligomères constituent la base des matériaux réticulés, influencent de nombreuses propriétés du matériau durci et composent entre 50 et 80 % de la formulation en poids.
- additifs – tous les autres composants ajoutés pour modifier les propriétés du mélange avant le durcissement ainsi que les propriétés du polymère après le durcissement. Les additifs comprennent, entre autres, des modificateurs de débit, des antimousses, des dispersants et des stabilisants à la lumière. Les additifs, avec les pigments, représentent la plus petite partie du mélange UV global.
- pigments – types spécifiques d’additifs qui donnent de la couleur aux formulations.
Les photoinitiateurs, monomères, oligomères, additifs et parfois pigments sont mélangés par les chimistes pour former des encres, des revêtements, des adhésifs et des extrusions durcissables aux UV. Des espèces de radicaux libres ou cationiques sont produites au sein de la chimie lorsqu’elles sont exposées à une combinaison optimale de longueur d’onde UV (nm) et d’irradiance (W/cm2). La photopolymérisation se produit très rapidement avec des temps de traitement se produisant en fractions de seconde. Le temps exact et la capacité du mélange à réticuler de manière appropriée dépendent du mélange de matières premières ; la puissance spectrale de la source émettrice (nm), l’irradiance (W/cm2) et la densité d’énergie (J/cm2) ; la demande ; la configuration de la ligne de production ; et l’utilisation de mécanismes de durcissement radicalaires ou cationiques. L’illustration suivante montre une formulation UV non durcie et la réticulation qui résulte lorsque la formulation est exposée à une source appropriée d’énergie UV.
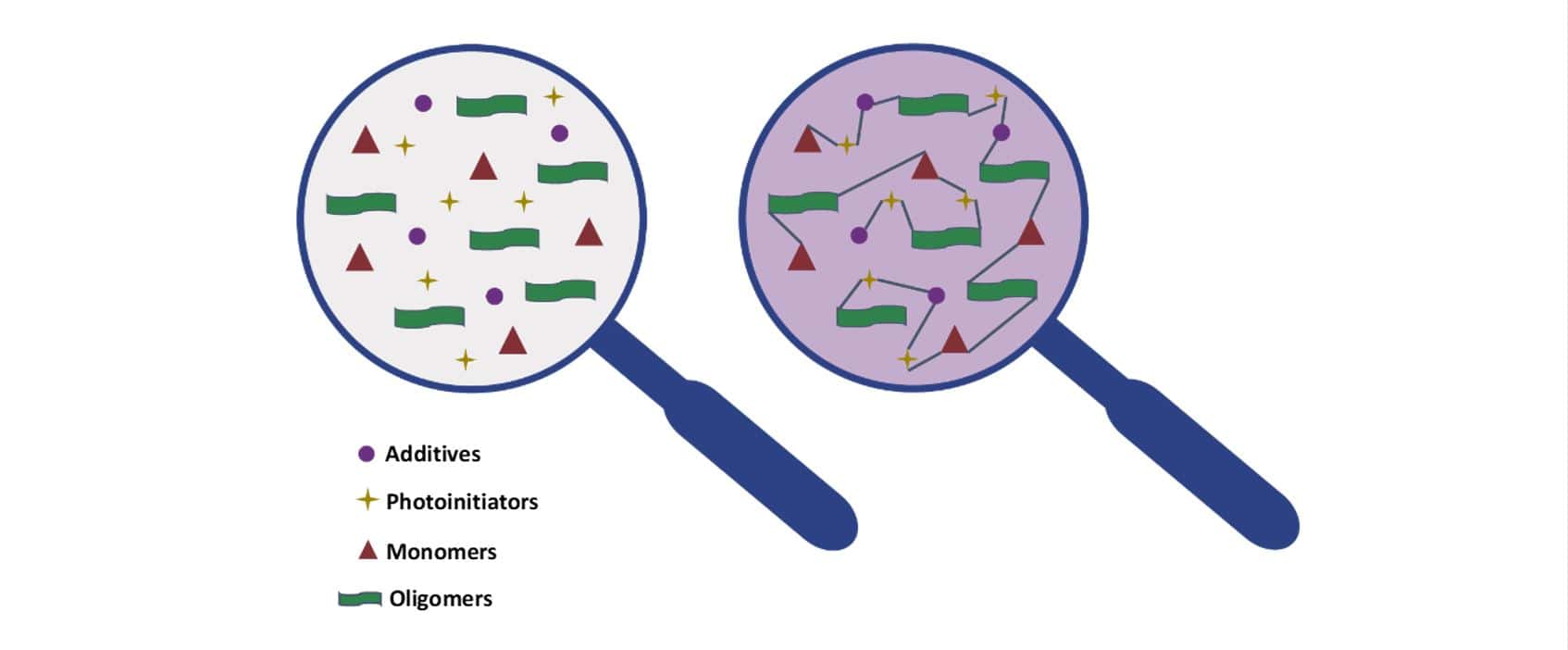
La nature liquide des formulations UV permet aux matériaux d’être extrudés ainsi que pulvérisés, projetés, distribués, roulés, trempés, imprimés, pulvérisés, aspirés ou inondés sur une large gamme de surfaces et de matériaux. Une fois appliquée, l’exposition à l’énergie ultraviolette est tout ce qui est nécessaire pour induire une réaction de propagation et de réticulation qui lie efficacement les molécules en structures solides homogènes.
Processus de durcissement UV
Les réactions de réticulation qui se produisent pendant le durcissement aux UV ne sont qu’une étape dans une séquence de nombreux processus de fabrication interdépendants qui se produisent avant et après le durcissement. Toutes les étapes doivent être identifiées, prises en compte dans le processus, évaluées pour déterminer leur impact les unes sur les autres, puis maintenues afin de produire systématiquement des produits répondant à la fois aux exigences de qualité et de performance d’utilisation finale.
Les étapes du processus liées au durcissement aux UV comprennent souvent :
- évaluation de la surface durcie – La forme, la structure, le type de matériau, la qualité du matériau, l’énergie de surface et la propreté de la surface durcie sont importants. Ces aspects déterminent si un prétraitement est nécessaire ; la formulation d’encre, de revêtement ou d’adhésif appropriée ; la manutention du matériel ; et l’orientation nécessaire de la tête de lampe UV. Les surfaces doivent être évaluées pendant le développement du processus et périodiquement pendant la production régulière.
- prétraitement et modification du substrat – Les surfaces des pièces et des matériaux doivent souvent être nettoyées, débarrassées de l’électricité statique ou traitées pour augmenter l’énergie de surface. Ces étapes sont souvent nécessaires pour faciliter le mouillage des encres, des revêtements et des adhésifs et pour améliorer l’adhérence. Les traitements comprennent le lavage ; bains ou lingettes chimiques; dispositifs antistatiques; l’application d’apprêts, de couches de base ou d’encollage ; flamme; couronne; plasma; ponçage; et le sablage, entre autres.
- manutention des matériaux – Les surfaces des matériaux sont généralement introduites dans les équipements de production sous forme de feuilles, de bandes ou de pièces tridimensionnelles. La manipulation du matériau doit permettre à l’encre, au revêtement ou à l’adhésif d’être appliqué uniformément sur la surface du matériau, puis exposé à une source UV à une distance décalée définie par rapport à la tête de lampe.
- Formulation d’encre, de revêtement ou d’adhésif – L’application, la surface du matériau, la méthode d’administration de la formulation, le système de durcissement et sa puissance UV, la vitesse de ligne ou la cadence de cycle et les exigences d’utilisation finale déterminent tous les propriétés nécessaires de la formulation. Il est important de partager ces détails avec les fournisseurs de formulations pour garantir que des formulations optimales sont utilisées.
- Équipement de distribution de formulations – Les encres, revêtements et adhésifs peuvent être appliqués de différentes manières au cours des processus de production, notamment par pulvérisation, jet, distribution, rouleau, trempage, transfert, pulvérisation, aspiration ou inondation. L’équipement d’application doit être adapté à la formulation, au type de pièce à polymériser ainsi qu’au matériau à partir duquel elle est fabriquée et à sa forme ou profil. La vitesse de la chaîne de traitement est également un facteur car elle détermine la densité énergétique requise.
- Évaporation des supports liquides – Une petite liste de formulations UV contiennent également de l’eau ou des solvants qui doivent être évaporés avant l’exposition à la lumière ultraviolette. Dans certains cas, la durée du trajet de la pièce jusqu’à la source de durcissement est suffisante pour que l’évaporation se produise, et dans d’autres cas, un mécanisme de séchage doit être intégré au processus pour accélérer l’évaporation.
- Polymérisation aux UV – La chimie des radicaux libres nécessite une exposition aux UV en ligne de mire directe, des longueurs d’onde UV adaptées aux photoinitiateurs présents dans la formulation, un seuil d’irradiation minimal qui s’adapte à la distance entre la lampe et la surface de polymérisation et une densité d’énergie suffisante pour polymériser à la ligne souhaitée. vitesse. Dans de nombreuses applications, un système de durcissement UV dédié est nécessaire pour chaque encre, revêtement et adhésif appliqué. Dans d’autres applications, plusieurs formulations peuvent être durcies simultanément avec une seule exposition de la tête de lampe.
- Équipement de traitement auxiliaire – De nombreuses applications de durcissement par UV nécessitent d’autres équipements pour faciliter le durcissement ou gérer les conditions du procédé. Cela comprend les systèmes d’inertie à l’azote, les rouleaux ou les plaques refroidies, les têtes de lampe ou les chambres de polymérisation à purge positive ou sous pression, les salles blanches, les optiques externes, les filtres UV et les systèmes de mesure UV intégrés.
- Traitement post-durcissement – Une fois la surface de la pièce ou du matériau durcie, elle nécessite souvent une conversion, une finition, un assemblage, un remplissage, un emballage et une expédition.
- Inspections de qualité – Chaque application a des spécifications de qualité et de performances différentes. Parfois, cela inclut la correspondance des couleurs. Dans d’autres, il pourrait s’agir de caractéristiques plus fonctionnelles. Des processus doivent être mis en place pour fournir des objectifs quantifiables qui peuvent être surveillés périodiquement pendant la production avec des variables de processus corrigées si nécessaire.
- Performance d’utilisation finale – Les conditions d’utilisation du produit final sont extrêmement importantes pour déterminer toutes les étapes de processus précédentes de cette liste. Il est important d’avoir des conversations concernant l’utilisation finale avec tous les fournisseurs liés au processus.
- qualifications, approbations et certifications – Les articles traités et durcis aux UV sont finalement fournis à un tiers qui peut avoir des exigences spécifiques qui dictent si le processus de production global est adapté à ses besoins ou aux objectifs de l’entreprise. L’obtention des qualifications, approbations et certifications appropriées de la part de l’acheteur, puis la tenue de registres d’inspection appropriés constituent souvent une étape vitale.
Bien que la liste à puces fournie représente un aperçu complet d’un processus de durcissement aux UV, elle ne constitue pas nécessairement une liste complète de toutes les activités possibles. Chaque application de durcissement UV et chaque ligne de fabrication UV auront des caractéristiques uniques qui peuvent introduire des étapes de processus non répertoriées. Dans tous les cas, il est toujours important d’évaluer les applications de durcissement UV, la ligne de fabrication où le processus doit être intégré, les activités de traitement post-durcissement et l’utilisation du produit final en tant que processus complet où chaque étape a potentiellement un impact sur les autres étapes. Heureusement, une fois le processus de durcissement UV établi, il est incroyablement fiable, reproductible et contrôlable.
Dans l’ensemble, le durcissement aux UV permet aux fabricants de fabriquer des produits dotés de propriétés physiques, mécaniques et esthétiques hautement souhaitables qui, à terme, améliorent l’apparence générale, la qualité et les performances de nombreux objets du quotidien. Comprendre les bases du durcissement UV, de la science de la lumière, de la chimie UV et des variables de processus facilite la sélection optimale de la source de durcissement UV et de la formulation, l’intégration appropriée, le contrôle du processus et la production cohérente de produits de qualité.